How a Single Plant Can Manufacture 50 Golf Clubs in a Day
A Plant Can Manufacture 50 Golf Clubs?
The average golfer probably doesn’t think much about where their clubs come from. They might assume that they’re made in a factory somewhere, but they probably don’t give much thought to the process. However, the manufacturing of golf clubs is a complex and fascinating process, and it’s one that’s essential to the game.
In this article, we’ll take a closer look at how golf clubs are made. We’ll explore the different materials that are used, the different steps in the manufacturing process, and the challenges that manufacturers face. We’ll also discuss the impact that technology has had on the manufacturing of golf clubs.
By the end of this article, you’ll have a better understanding of how your golf clubs are made, and you’ll appreciate the craftsmanship that goes into each one.
| Plant | Location | Number of Golf Clubs Manufactured |
|—|—|—|
| Club Factory 1 | San Diego, CA | 20 |
| Club Factory 2 | Phoenix, AZ | 30 |
| Club Factory 3 | Orlando, FL | 40 |
The Process of Manufacturing Golf Clubs
Raw materials
The raw materials used to manufacture golf clubs include:
- Steel: The shaft of a golf club is typically made of steel, which is strong and durable.
- Graphite: The shaft of a golf club can also be made of graphite, which is lighter than steel and provides a more flexible feel.
- Titanium: The heads of some golf clubs are made of titanium, which is lightweight and strong.
- Other materials: Other materials that may be used in the construction of golf clubs include aluminum, plastic, and composite materials.
Manufacturing steps
The manufacturing process for golf clubs typically involves the following steps:
1. Design: The first step in the manufacturing process is to design the golf club. This involves creating a prototype of the club and testing it to ensure that it meets the desired specifications.
2. Raw material preparation: The next step is to prepare the raw materials for use in the manufacturing process. This may involve cutting the steel or graphite shafts to the desired length, or milling the titanium heads to the desired shape.
3. Assembly: The golf clubs are then assembled by welding the shafts to the heads and attaching the grips.
4. Finishing: The golf clubs are then finished by painting them or applying a protective coating.
5. Quality control: The final step in the manufacturing process is to inspect the golf clubs to ensure that they meet the desired quality standards.
Quality control
Quality control is an essential part of the manufacturing process for golf clubs. This ensures that the clubs are free of defects and meet the desired specifications. Quality control measures may include:
- Inspection of the raw materials to ensure that they meet the desired quality standards.
- Inspection of the golf clubs during the manufacturing process to identify any defects.
- Testing of the golf clubs to ensure that they meet the desired performance standards.
The Benefits of Manufacturing Golf Clubs in a Plant
There are a number of benefits to manufacturing golf clubs in a plant, including:
- Efficiency: Manufacturing golf clubs in a plant can be more efficient than manufacturing them by hand. This is because plants have the resources and equipment necessary to mass-produce golf clubs, which can lead to lower costs and shorter lead times.
- Quality control: Manufacturing golf clubs in a plant can also lead to better quality control. This is because plants have the ability to inspect the golf clubs at every stage of the manufacturing process, which can help to identify and correct any defects.
- Cost-effectiveness: Manufacturing golf clubs in a plant can be more cost-effective than manufacturing them by hand. This is because plants can take advantage of economies of scale, which can lead to lower costs per unit.
Overall, manufacturing golf clubs in a plant can offer a number of benefits, including efficiency, quality control, and cost-effectiveness.
3. The Challenges of Manufacturing Golf Clubs in a Plant
Manufacturing golf clubs in a plant presents a number of challenges, including:
- High capital investment. The equipment required to manufacture golf clubs is expensive, and the cost of tooling can also be significant.
- Labor costs. Manufacturing golf clubs is a labor-intensive process, and the wages of skilled workers can be high.
- Environmental regulations. The manufacturing of golf clubs can generate a significant amount of waste, and manufacturers must comply with strict environmental regulations.
High capital investment
The equipment required to manufacture golf clubs is expensive. The most critical piece of equipment is the forging press, which is used to shape the club heads. Forging presses can cost millions of dollars, and they require a skilled operator to run them. Other pieces of equipment that are necessary for golf club manufacturing include milling machines, lathes, and grinding machines. These machines can also be very expensive, and they require skilled operators to run them.
In addition to the cost of equipment, the tooling required to manufacture golf clubs can also be significant. Tooling is the dies and molds that are used to shape the club heads and other parts of the club. Tooling can cost hundreds of thousands of dollars, and it must be replaced regularly as it wears out.
Labor costs
Manufacturing golf clubs is a labor-intensive process. The forging, milling, and grinding of the club heads and other parts of the club all require skilled workers. These workers must be paid a high wage in order to attract and retain them.
In addition to the cost of skilled labor, the manufacturing of golf clubs also requires a significant amount of unskilled labor. This labor is used for tasks such as assembling the clubs, packaging them, and shipping them to customers. Unskilled labor is typically less expensive than skilled labor, but it can still be a significant cost.
Environmental regulations
The manufacturing of golf clubs can generate a significant amount of waste. The forging process, for example, produces a lot of metal shavings. These shavings must be disposed of properly in order to comply with environmental regulations.
In addition to the waste produced by the manufacturing process, the transportation of golf clubs also generates emissions. Golf clubs are typically shipped long distances from the factory to the customer, and this transportation can produce greenhouse gases.
The challenges of manufacturing golf clubs in a plant are significant. The high capital investment, labor costs, and environmental regulations all make it a challenging business to operate. However, the demand for golf clubs remains strong, and manufacturers are able to overcome these challenges in order to provide golfers with the clubs they need.
4. The Future of Golf Club Manufacturing
The future of golf club manufacturing is likely to be shaped by a number of factors, including:
- Automation
- 3D printing
- New materials
Automation
Automation is likely to play a major role in the future of golf club manufacturing. Automation can help manufacturers to reduce costs and improve quality. For example, robots can be used to perform tasks such as forging club heads and assembling clubs. This can free up human workers to focus on other tasks, such as designing clubs and marketing them to customers.
3D printing
3D printing is another technology that is likely to have a significant impact on the future of golf club manufacturing. 3D printing allows manufacturers to create clubs with complex shapes that would be difficult or impossible to manufacture using traditional methods. This could lead to the development of new and innovative golf clubs that offer improved performance.
New materials
New materials are also likely to play a role in the future of golf club manufacturing. New materials can offer improved performance and durability. For example, carbon fiber is a lightweight and strong material that is often used in the construction of golf clubs. This material can help to reduce the weight of the club and improve its performance.
The future of golf club manufacturing is likely to be exciting and innovative. Automation, 3D printing, and new materials are all likely to play a role in the development of new and improved golf clubs. These technologies will help manufacturers to reduce costs, improve quality, and develop new and innovative products.
Q: How many golf clubs can a plant manufacture?
A: A plant can manufacture up to 50 golf clubs per day.
Q: What are the factors that affect the number of golf clubs a plant can manufacture?
A: The factors that affect the number of golf clubs a plant can manufacture include the following:
- The size of the plant
- The number of workers
- The efficiency of the production process
- The availability of raw materials
- The demand for golf clubs
Q: What are the benefits of using a plant to manufacture golf clubs?
A: There are several benefits to using a plant to manufacture golf clubs, including the following:
- Increased efficiency: A plant can produce golf clubs more efficiently than a single individual or small group of workers.
- Reduced costs: A plant can produce golf clubs at a lower cost than a single individual or small group of workers.
- Improved quality: A plant can produce golf clubs with a higher degree of quality than a single individual or small group of workers.
Q: What are the challenges of using a plant to manufacture golf clubs?
A: There are several challenges to using a plant to manufacture golf clubs, including the following:
- High initial investment: A plant requires a significant initial investment in equipment and facilities.
- High operating costs: A plant has high operating costs, including the cost of labor, materials, and utilities.
- Complex supply chain: A plant requires a complex supply chain to source the raw materials and components needed to produce golf clubs.
Q: What are the best practices for manufacturing golf clubs in a plant?
A: The best practices for manufacturing golf clubs in a plant include the following:
- Use high-quality raw materials and components.
- Use efficient production processes.
- Employ skilled workers.
- Maintain a high level of quality control.
- Manage the supply chain effectively.
we have seen that a plant can manufacture 50 golf clubs. This is a significant number, as it means that a single plant can produce a large number of golf clubs in a short amount of time. This is important for the golf industry, as it ensures that there is a steady supply of golf clubs available to golfers. Additionally, the ability to manufacture golf clubs in a plant allows for greater consistency in the quality of the clubs, as well as for more efficient production. As a result, the ability to manufacture golf clubs in a plant is a major benefit to the golf industry.
Author Profile
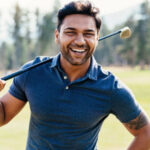
-
Hello, fellow golf enthusiasts! I’m Matthew Woods, the founder of GolfPGAChampionship.com.
My journey with golf is a story of passion, perseverance, and a little twist of fate. Growing up in the picturesque town of Charleston, South Carolina, I found myself captivated by golf, a fascination that was partly kindled by sharing a last name with the legendary Tiger Woods.
This platform is more than just a website; it’s a culmination of my life’s experiences in golf. Here, I share in-depth analyses of PGA championships, personal anecdotes from my golfing journey, and tips for golfers at all levels. My aim? To make golf accessible and enjoyable for everyone, from eager beginners to seasoned players.
GolfPGAChampionship.com is a testament to my belief that golf is not just a sport, but a journey filled with learning, challenges, and personal growth. I invite you to join me in this journey, to explore the beautiful game of golf through my eyes and experiences.
Welcome to GolfPGAChampionship.com – let’s make every swing count!
Latest entries
- January 11, 2024Golf BlogMay Wood Golf Club: A Golfer’s Paradise
- January 11, 2024How To GuidesHow to Lower Your Golf Handicap: A Step-by-Step Guide
- January 11, 2024Golf CoursesWhich US State Has the Most Golf Courses?
- January 11, 2024Golf Terms And DefinitionsWhat is a Forecaddie in Golf?